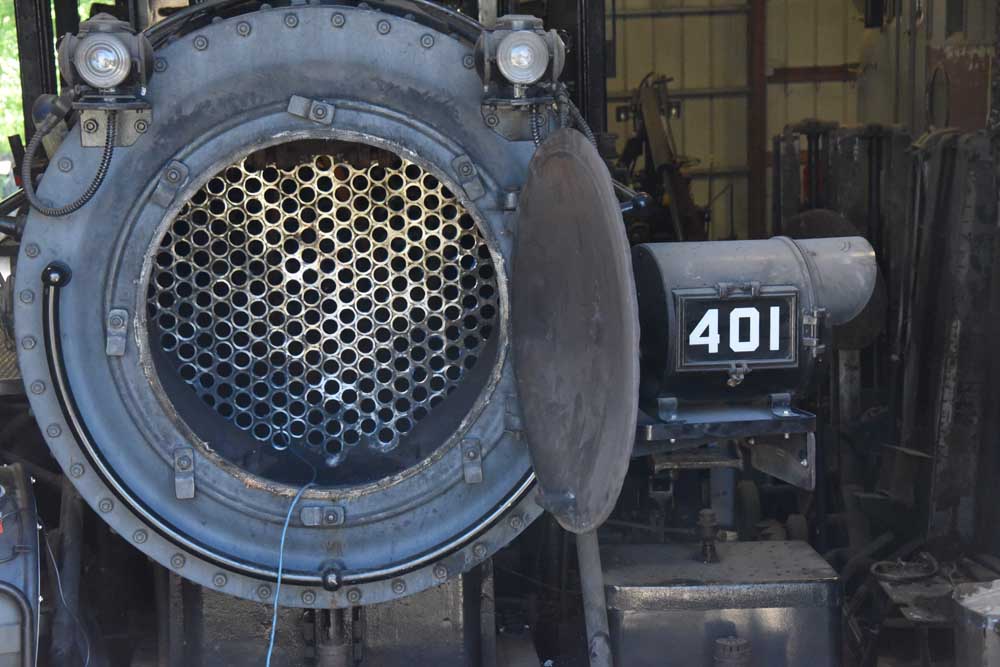
Locomotive flue sheets are an important component in a steam locomotive’s design. The steam-generating part of every conventional steam locomotive consisted of three elements — the firebox where the fuel was burned to provide the heat, the boiler itself where water was converted into steam, and the smokebox where the exhaust from the engine was used to provide draft for the fire. There the exhaust was combined with the gases resulting from the combustion of the fuel and expelled into the atmosphere.
Locomotive flue sheet locations
The firebox was designed so that it was surrounded by water on all sides and at its front end was separated from the boiler by a flat sheet of steel called a flue sheet. A similar flue sheet riveted to the first boiler course enclosed the boiler at its front end, thus sealing the boiler itself so that pressure could be attained.
These locomotive flue sheets were connected by boiler tubes or flues which allowed passage of the gases from the combustion to flow forward into the smokebox and then expelled into the atmosphere.
A large locomotive boiler would have well more than 200 of these tubes, plus possibly 40 or so larger tubes at the top for the superheater units; the superheater units extended into these larger tubes from the superheater header ahead of the front flue sheet. The superheater units were thus subjected to the fire, raising the steam temperature well above the normal figure for the pressure. This extra heat was recovered as additional work in the cylinders.
Flue sheet stressors
These flue sheets had to withstand not only the pressure in the boiler which might be 300 pound-per-square-inch or more, but the rear sheet was exposed to the direct heat from the fire which might be well more than 2,000-degrees Fahrenheit.
The front flue sheet had its own stresses; not only did it have the boiler pressure on its back side, but it was subjected to a rhythmic pulsating vacuum on its front side from the exhaust from the cylinders; this vacuum provided the draft for the fire by pulling the fire through the flues and tubes.
If you saw one of these flue sheets laid out in the boiler shop before application it might look like it had more holes than sheet, with those two hundred plus holes for the tubes the front flue sheet had a large hole at its top for the steam pipe from the steam dome to pass into the superheater header. In the case of a locomotive with a dome throttle this steam would be divided and passed to the two cylinders.
The tubes and flues were sealed into the sheets by welding. They were a high-maintenance item and were required to be replaced every three years.
Two more interesting things about flue sheets…….The tubes and flues were first sealed by rolling, wherein the tube was tightly expanded into the hole with a tube roller, which consists of three tapered hardened pins, driven by a central reverse-tapered driver pin. The riolling can be done by hand with a wrench, but railroad shops typically used an air-powered driver. After rolling, the edges of the tubes were “beaded” over, again with an air-hammer and special bit, to protect the fire-ends from eroding and to guarantee the tube could not let go of its grip on the tube sheet. Welding the fire ends was done as a seal, because of the wide temperature variations that end of the tube had to endure. The smokebox ends usually weren’t weld-sealed.
The stresses from heating & cooling, and yes the pulsating exhaust vacuum could manifest itself in cracks developing between the tube holes, and also around the edge, where the sheet was flanged for riveting to the boiler shell. Such was the case with East Broad Top #16, currently undergoing restoration. The edges had so many cracks, that a new front flue sheet had to be fabricated.