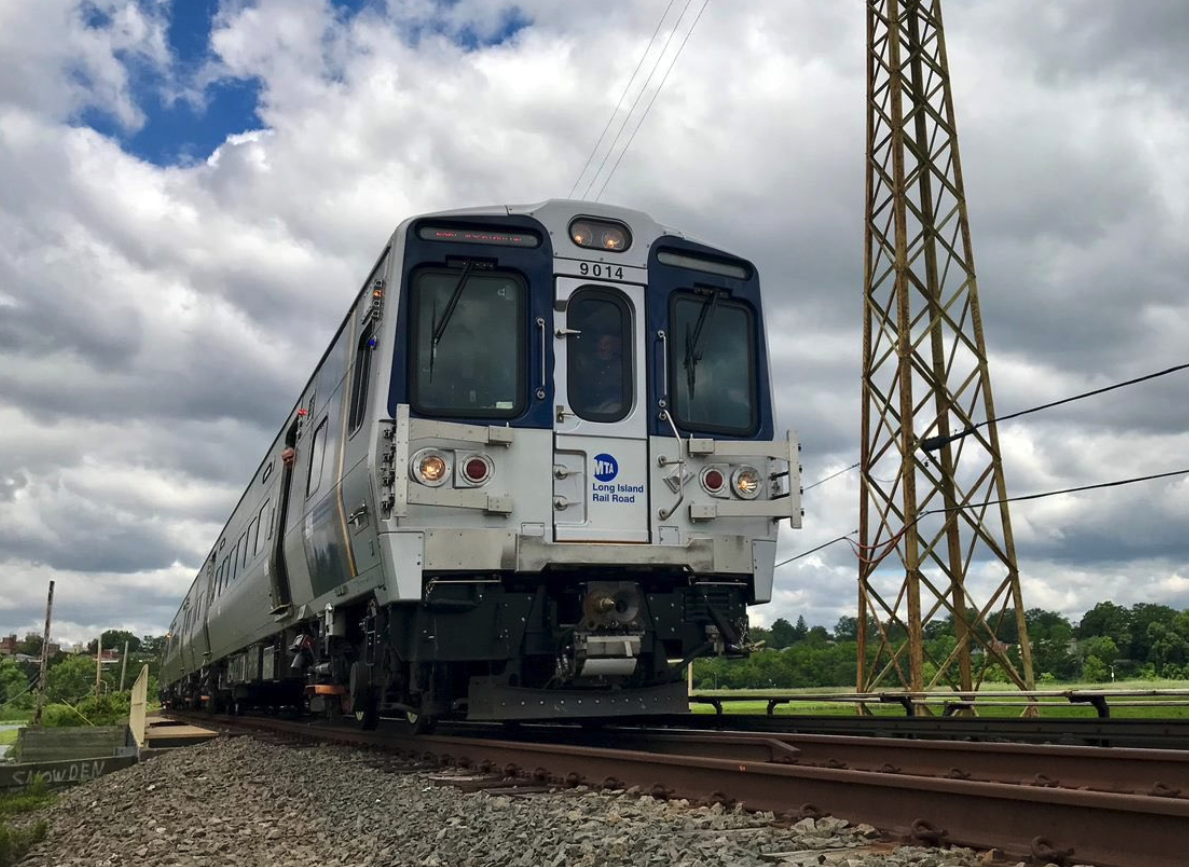
NEW YORK — An initial order for new electric multiple-unit railcars for the Long Island Rail Road fell almost three years behind schedule and more than $8.9 million over budget — and the commuter railroad failed to collect damages and accepted cars with defects that were not repaired in a timely fashion, according to a state audit report.
In a response, the LIRR said it “fundamentally disagrees with the audit conclusions.”
The report from the office of New York State Comptroller Thomas DiNapoli examines the acquisition of M9 EMU railcars from Kawasaki from the time the order was placed in September 2013 to the point until November 2020, by which time 64 of the 92 cars in the original order had been conditionally accepted. The LIRR also exercised an option for 110 additional cars in July 2017. A report summary is available here; the full report, including the LIRR response, is here.
According to the report, LIRR officials say the M9 project is behind schedule because of an accident in delivering eight pilot cars, and because of testing at the Federal Railroad Administration test center in Pueblo, Colo. The audit found that issues discovered during the testing in Pueblo were not corrected before additional cars were delivered with the same problems.
Cars accepted with defects which have not been fixed
The report also says the LIRR contributed to the problem by accepting cars with deficiencies under a “conditional acceptance” process in the contract, It says the commuter railroad identified manufacturing issues including inadequate employee training at the company’s Nebraska factory, ineffective inspections prior to delivery, and inadequate staffing at the final assembly facility in Yonkers, N.Y. While the LIRR said it outlined corrective action, the report found these actions were not effective.
As of Aug. 13, 2020, the LIRR had accepted 62 railcars with a total of 9,230 defects or deficiencies — none of which are safety-related, the railroad says. Over a year later, those defects had not been corrected, nor had the LIRR set a deadline for the builder to do so. With the contract running almost three years behind schedule, the LIRR is focused on delivery of the remaining cars, not fixing defects on those delivered. “The continued operation of railcars with minor defects and deficiencies runs the risk of aggravating the defects over time into conditions that will impact the operations of the railcars and result in increased repair costs,” the report says.
Report says millions in damages have not been assessed
The contract with Kawasaki provides for liquidated damages; a subsequent contract revision set damages at a flat rate per car, per calendar day of delay, beginning 30 days after the a date set for each car in the contract, until its acceptance or conditional acceptance. Under the original contract, these damages were almost $12.9 million as of January 30, 2019, but the revised contract waved those damages and required the LIRR to pay $18.8 million to resolve outstanding claims. Under the revised contract, the LIRR was in position to assess $5.5 million in damages as of Sept. 11, 2020, a number expected to reach $12 million for the first 92 cars. The LIRR said its practice is to access damages at the end of a contract; the audit contends the LIRR should act earlier “to prod the contractor to improve its performance.”
The report also found the LIRR had not ensured software testing had been performed as required, and that it did not follow contractor evaluation guidelines. It outlines a total of 12 recommendations to address the issues identified by the audit.
LIRR response takes issue with most points
The response from LIRR President Phillip Eng says the commuter railroad “strongly disagrees that it contributed to the delays by accepting cars with deficiencies,” saying this is an industry practice with non-safety related minor defects, and that it assists in expediting the delivery schedule. It also says that contrary to the audit report, its remedial actions with the manufacturing problems were effective.
While the audit claims there are $8.9 million on overruns, the LIRR contends no overruns exist because the contract combines both the phases of the contract instead of breaking out the initial order, as was done in the audit. It also says it is inaccurate that the LIRR did not assess damages, as those damagers were part of a negotiated settlement.
On the matter of unaddressed defects, the LIRR says that because cars must be taken out of service to be modified, “it is to LIRR’s benefit to combine as many modifications as possible so the cars come out of service as few times as possible.” It also says the report “dramatically overstates” the significance of operating cars with minor defects.
From my viewpoint, it’s not just defects that I worry about. There are things that LIRR specs out that are of concern. One is that while you can plug in for power, you’ve got to reach across your seatmates to do so, and have, as I recall, a brick for that. The person sitting against the outer wall – do they have these bricks blocking their movement, or sticking into their sides?
Then there is the seating. On the M7’s and C3’s, you have painfully uncomfortable headrests, with ‘points’ sticking out into the back of your head, super hard, and your head bouncing against and between them. Arm rests that hurt your arms. The back of the seat in front of you is super hard – so it is painful to brace your knees against it. MTA knew how bad this was before most of the C3 cars were built, and refused to do anything about it. They chose to do the same thing in the M7’s. I’m told that the M9’s are just as bad.
Supposedly MTA will one of these decades order new diesel locos (DE and DM) which I’m guessing will be just as unreliable as the current fleet – something avoidable, of course. And new passenger cars for those locos. Probably double decker. I’m guessing, as they did in the mid 1990’s, that these will also be a few inches too big to fit in the ESA tunnels. Since it will likely be decades before diesel country is electrified (yes, supposedly they are looking at that for the PJ line – a line that needs a lot more than that), odds are that I won’t live to see direct trains to GCT from out east, nor will most of us.
I don’t know who makes these decisions at MTA, but I’m guessing that they take after Robert Moses, and a onetime PA chair some years back who never, ever boarded or used mass transit.
Why would anyone or agency accept a product with defects. Would an average individual accept delivery of a car/truck without headlights or windshield wipers. Hell no. The person/persons who signed off on delivery of the defective rail cars should have been fired.
The “price” of low price.
It seems that somewhere at L.I R.R., Kawasaki has power over someone to make them not want to do what’s best for the railroad. I would have taken Kawasaki to task to fix the problems and pay for the delays. Office mates remember me yelling into the phone “Bull S@%t” when a vender was telling me that something was an extra charge when I had it included in the contract that had been accepted.
This is the result when you have an audit done by an authority that has ZERO knowledge of the commodity/agency they’re auditing.