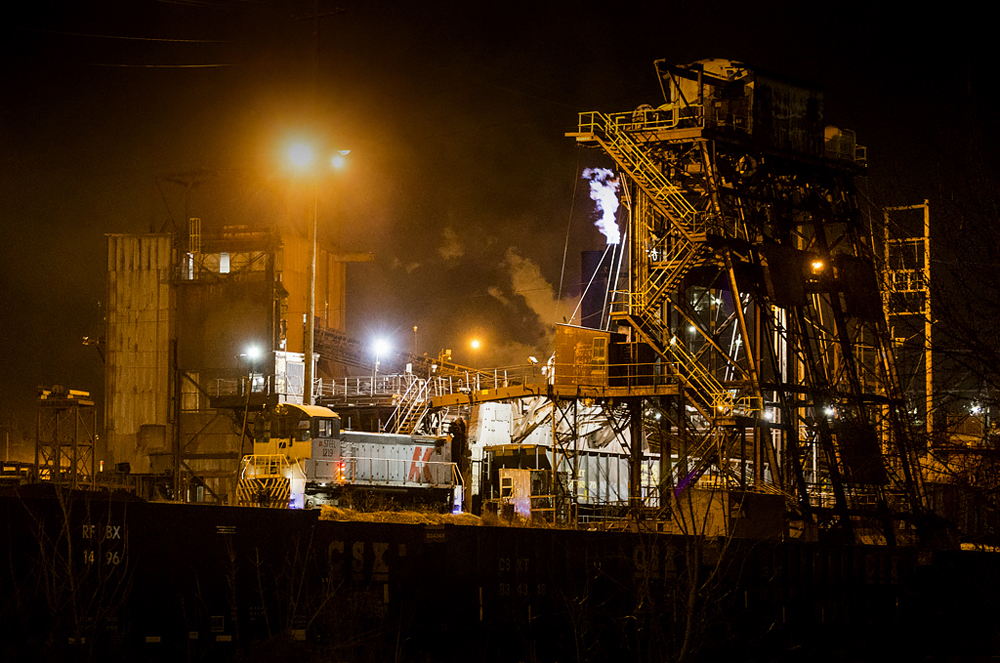
CHARLESTON, W.Va. — Industrial manufacturing is on the rise and the demand for U.S. steel is driving steel prices and railcar loadings above pre-pandemic levels, but don’t expect U.S. steelmakers to open idled operations.
According to the Association of American Railroads’ weekly railcar traffic report, shipments of metallic ores and metals were up to 22,369 carloads the week ending Oct. 9, 2021 — representing a 28% increase from the same period in 2020. For the year, that commodity group is up to more than 908,000 carloads, or about a 27% increase from 2020 year-to-date numbers. This double-digit growth isn’t unexpected given widespread uncertainty surrounding COVID-19 this time a year ago.
But when you analyze the pre-pandemic equivalents, metals shipments by rail are up 18% for the week, with railroads having handled just shy of 18,900 carloads the same week ending on Oct. 5, 2019 — a positive difference of around 3,400 carloads. Year-to-date comparisons from 2019 and 2021 show that U.S. railroads have handled about 3% more volume, indicative that steel demand is strong and is benefiting railroads. Rail shipments of metallic ores consist of ores, coke, metal products, and iron and steel scrap.
According to the American Iron and Steel Institute, U.S. steel makers produced 8.4 million tons in August, up 28% from 6.5 million tons in 2020. Year-to-date steel production through the first eight months of 2021 still trails the pre-pandemic numbers of 2019 by about 11 million tons. This is likely due in part to U.S. steel makers idling higher-cost facilities prior to and during the onset of COVID-19 that have not reopened, further driving demand and prices higher amid tight supply.
The Wall Street Journal reported in June, citing industry consultants, that domestic producers U.S. Steel Corp. and Cleveland-Cliffs, Inc. had approximately 7 million tons of production capacity out of service. This included older mills and blast furnaces that producers say are more costly to operate.
In December 2019, three months before the pandemic shuttered the economy, U.S. Steel announced its plans to indefinitely idle most of its Great Lakes Works operation in Ecorse, Mich. And in March 2020, U.S. Steel idled two blast furnaces at its Granite City, Ill., mill, but restarted one blast furnace at a later date.
Demand is high, but the economics of reopening idled mills and blast furnaces still come with a high cost and are unlikely to occur. Instead, steelmakers are likely to continue producing at-near capacity numbers at existing facilities and will channel future investments in lower-cost electric furnaces. In September, U.S. Steel announced that it was looking for a site to build a state-of-the-art mini mill at an estimated investment of $3 billion. It is expected to begin production in 2024, although a final location has not been announced.
Today’s steel prices are flirting around $1,600 per ton, up from $540 per ton at the onset of COVID-19, and up from a pre-pandemic average of around $1,000 per ton, according to the American Steel Index.
Ongoing demand and record-prices indicate that steelmakers and railroads, which haul both raw materials inbound and finished products outbound, are likely to see strong performance in the foreseeable future, with the industry gradually shifting to newer, lower-cost operations over time.
Charles, there is a new process using hydrogen, not sure how it works but it replaces the need for the coal in the process. Being used in Europe already and already at least one large North American producer is embarking on a seven year conversion to their process to switch from coke ovens / blast furnaces / BOF to pure EAF.
Remember the main purpose of metallurgy coal is to make coke which becomes the fuel in the blast furnace. Obviously adds carbon to the iron as well.
There is also a process the iron ore processors are doing to help with the carbon content in the pellets for use in EAF melting.
When I worked in steel making, coke fines were added to the ladle to adjust the carbon content at the end of the melting process. I can see there still being the need for this but again I am not sure.
Happily retired now.
DRI, direct reduction iron is the process being used for the iron ore being melted in EAF steelmaking.
There are many positives to moving to the EAF steelmaking process, it is overall more efficient use of energy, requires much less capital to build and maintain, and almost if not completely eliminates the need for metallurgic coal due to no coke ovens and blast furnaces.
So as there is considerable pressure to reduce coal consumption this is a major step.
However while on the topic of coal, the EAF process does require a considerable amount of electrical power so it is hard to say what the net environmental savings will be if coal generated power has to increase. The new mill location will play an important part since cheap power is a major consideration when building an EAF facility.
I can understand EAF for melting scrap to form new steel. What about if you are making steel from iron ore; don’t you need coal in the process in order to mix the carbon with iron to form steel?
If the money that would be spent starting up older, inefficient mills is used to to build newer mills that are more efficient and better aligned to current demand, than isn’t that a good thing? It sounds like that may be at least partially what is going on here. 2024 is a long way off, but if the end game results in better mills, than it is game that is worth playing.
Just another example of the Harvard/Chicago/Wharton business school education at work. That’s how to make America (not so) great.