It might be a warm summer morning in the early 1950s on the Illinois Central near Clinton, Ill.; or maybe a cold January day along the Pere Marquette outside of Grand Rapids, Mich. There’s the sound of a fast-running steam locomotive in the distance … the railroad’s in a hurry with something today. Shortly an engine and an unusual 5-car train blast into town. Amazingly, as the special roars by, the rear car disconnects from the train! Brakes can be heard; the car and the rest of its train come to safe stops a half-mile down the line. You’ve just gotten a rare glimpse of a unique operation — the American Steel Foundries test train.
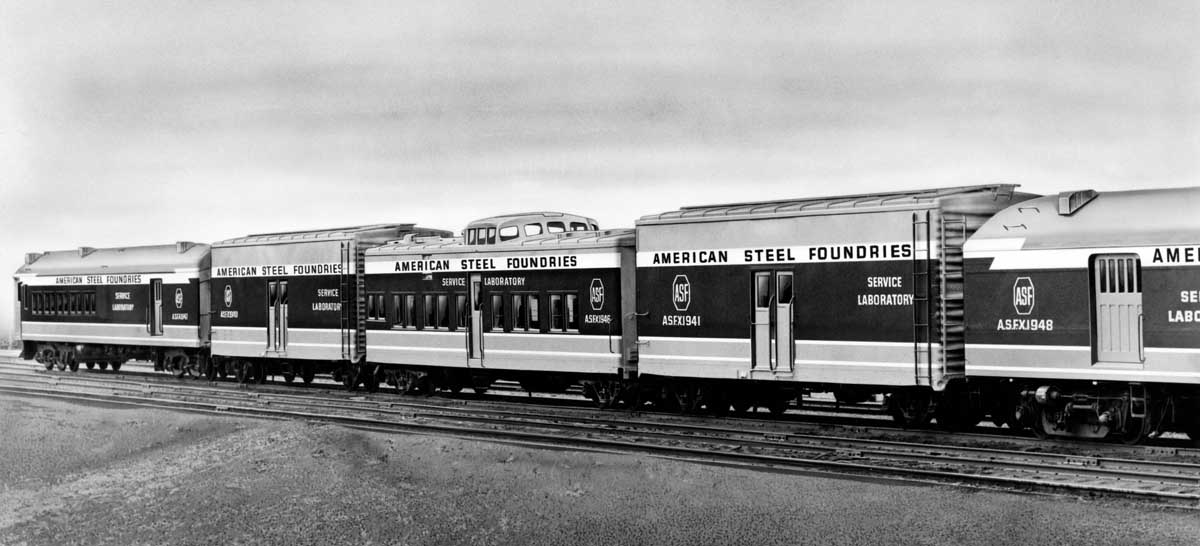
ASF’s rolling “service laboratory” was the culmination of years of research aimed at improving the operation of the trucks and brakes on freight and passenger cars, leading to the success of the company’s A-3 Ride Control freight-car truck. This research and development work dates back to the early 20th century, with the creation of a company testing lab equipped to simulate and design for the increasing speeds and loads encountered by freight-car trucks. Such lab-based work provided valuable insight, and some testing was done on instrumented freight cars to correlate that work in real-world conditions.
In 1931 the Chicago-based company put together a train of four loaded coal hopper cars, a caboose, three test cars, and a second caboose equipped with recording instruments. Chicago & North Western was the host railroad, operating the train at speeds up to 60 mph on the main line west to Clinton, Iowa. This train and its accompanying technicians were the company’s first version of a dedicated set of equipment for real-world testing.
A further step came in 1940 with the purchase of two standard boxcars. These cars were then fitted with glass windows in the floors to permit viewing wheel and truck performance at speed, and cranes and fixtures to permit loading heavy weights. State-of-the-art instrumentation was installed to measure and record speed, spring deflections, and vertical and lateral movements of the trucks and the carbodies. A 5 kW generator and batteries provided electrical power, and phone jacks throughout the cars facilitated communications among the technicians.
Important details were attended to, such as attaching instruments directly to the cover plates of the carbody bolsters to eliminate any potential cushioning from the wood flooring. “V-shaped” bay windows allowed technicians to observe and record track conditions, switches, curves, and grade crossings. Even the weather conditions were carefully documented, as performance had to be evaluated in all extremes of temperature and precipitation.
One of the boxcars, with conventional trucks, provided a standard with which to compare data taken on the other car, which was equipped with the new or modified components being evaluated. At this stage in the American Steel Foundries test train’s development, technicians worked and lived in a variety of conditions. Sometimes the host railroad provided a coach and a baggage car for additional test equipment and the train operated on its own; other times the two boxcars were simply added to a regular freight train with technicians sharing the caboose with the train crew.
The first high-speed test runs made with these special boxcars were on the Milwaukee Road between Milwaukee and Portage, Wis. Interlaced with the road’s famous Hiawatha speedsters, a total of 55 runs were made from August to November 1940 at speeds up to 95 mph. Similar speeds were attained during test runs on Missouri Pacific’s Arkansas Division in 1941. The train logged 8,480 miles on the New York Central between Englewood (Chicago) and Elkhart, Ind., and by the end of 1945 many more miles had been run on Santa Fe, C&NW, and Great Northern.
Serving on board the test cars was challenging, as the technicians were exposed to the noise and temperature conditions of high-speed freight railroading. Scheduling the test train amid the heavy traffic of World War II and postwar prosperity meant long waits followed by quick responses to short time windows. Through it all, instruments had to be maintained in calibration and data preserved for later analysis in the engineering offices.
The following year, 1946, saw the introduction of an operations car built from a Pullman troop sleeper and fitted with a cupola. This car was an improvement over borrowed baggage cars and allowed equipment and wiring cables to be more efficiently laid out in fixed positions. The operations car was placed between ASF’s two test boxcars during test runs.
In 1947 the company purchased two combination coach-baggage cars. One served as a buffer between the locomotive and the first boxcar, as well as to house the technical crew and to store equipment. The second combine was at the rear of the five-car train and was equipped for special passenger-car brake tests. Equipment was included to permit wetting and/or sanding the rails to simulate actual service conditions. At speeds up to 115 mph, the rear car could be uncoupled for breakaway tests, checking stopping distances, wheel slip, deceleration rates, and brake-pipe air-pressure changes. Various designs of brake rigging were tested as well as comparison tests of clasp (shoe) brakes versus disc brakes on wet and dry rail.
Starting with those first high-speed runs on the Milwaukee Road, until October 1952, the American Steel Foundries test train made 994 runs and logged a total of 145,842 miles. In the late 1950s, more sophisticated equipment led the company to expand its testing laboratories, and the test train eventually was eased into retirement. ASF successor Amsted Rail owes its leadership position in the railroad supply industry to the developments perfected on the test train. Through the data recorded and test results obtained aboard the rolling laboratory, improvements in spring packages, side frames, bolsters, and brake rigging made it possible to satisfy a variety of speed and loading needs for safe operation of railroads around the world.
Great article–something completely new to me. The mechanical engineers must have loved being able to test theories and collect data and observations in (relatively) real-life operation. More articles like this–historical and present-day–would be good to see.
Would like to see more info on the test cars and an update on technology from 1950’s thru the year 2000, or beyond. Very interesting article.