Track ballast
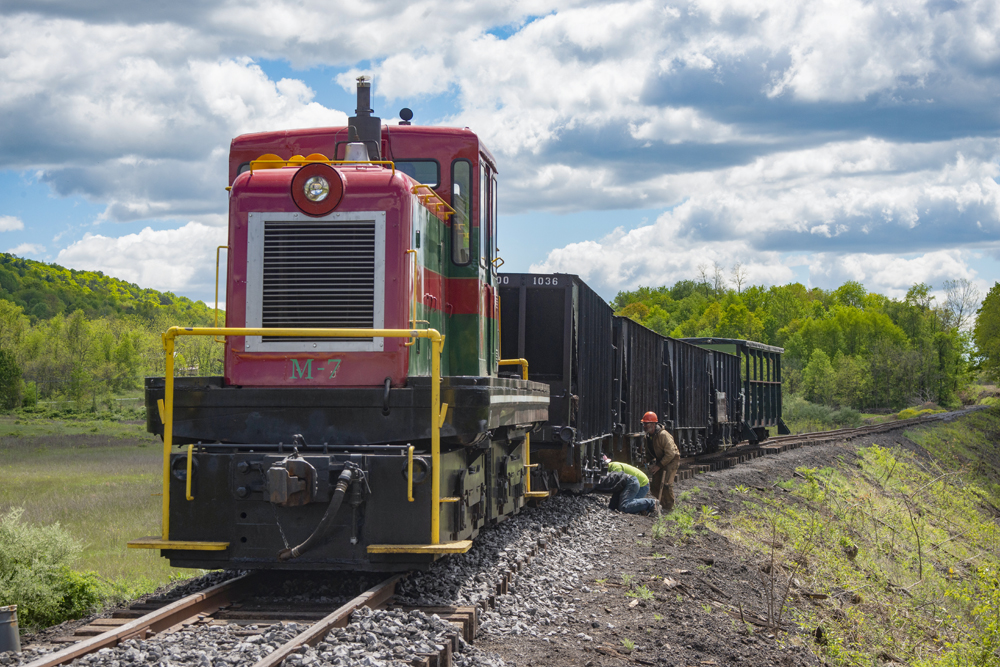
Down below the trains, below the rails, the tie plates, and the ties, is a lowly yet vital component of railroading — track ballast. While ballast may not be at the top of anyone’s list of rail topics, it’s literally part of the foundation of railroads, and it can comprise more than 80% of the weight of the track structure.
Track ballast performs several important functions:
- It distributes weight.
- It keeps the ties in place.
- It allows water to drain away.
- It protects track from the effects of frost heaving.
- It facilitates maintenance by keeping track up off the ground.
- It retards the growth of vegetation.
- It provides firm yet resilient support.
Distributing weight
A key job for ballast is to transmit the weight (or “load”) of the track and, more significantly, the trains passing over it, to the subgrade. These loads produce pressures averaging 100 pounds per square inch underneath each tie, far greater than earthen subgrades can bear on a repeated basis without settling. (Some soils can take pressures of 50 PSI regularly, but many have endurance limits of far less.)
Ballast serves to distribute the tremendous loads over an area of subgrade large enough to bear them without undue settling. Without track ballast, the ties would sink unevenly into the subgrade. As cars have gotten heavier, their loads have had to be dispersed over larger areas.
While ballast often did not cover the ends of ties on mainline track 50 years ago, “shoulders” of ballast extending 12 to 18 inches beyond the tie ends are common today.
Another task of ballast is to inhibit the lateral and longitudinal movement of the ties. The irregularly shaped ballast particles interlock with the ties and with each other to resist tie movement, which can lead to uneven support and misalignment of track.
Battling the elements
Railroad track, like buildings, needs good drainage to remain in top condition for long periods. Ballast provides immediate drainage of water away from the rails and ties. This is accomplished by its cross-section (the ends of which have a slope of about 1 foot of rise for every 2 feet of run) and by the porous, free-draining properties of ballast materials. Should poor drainage cause ballast to remain wet, it can cause problems by freezing in the winter, thawing in the spring, and fostering plant growth in the summer.
Frost heaving of the subgrade, which can cause track to become uneven, is reduced by ballast. The removal of moisture through draining eliminates a prime cause of heaving, while the presence of relatively wide voids between ballast particles eliminates movement of moisture from the ground up. Also, there is a certain amount of elasticity to ballast, which absorbs subgrade heaving.
Track maintenance is facilitated by the presence of ballast. With a flexible, easily worked medium between the track and the subgrade, track leveling and other tasks are more easily accomplished.
The growth of vegetation, undesirable because of the deleterious effects it has on track drainage, is retarded by the presence of ballast. The good drainage provided by ballast removes the moisture necessary for most plant growth, and new ballast material contains little or no clay or silt in which plant growth may develop.
Flexible rock
While ballast provides track with firm support, it is not absolutely rigid. Each axle of a loaded, 100-ton car will deflect even the stiffest track about one-tenth of an inch, and relatively soft track will give as much as a half-inch.
Ballast is meant to possess a resilience that absorbs some of the shock from the “dynamic loading” of passing trains. The rough particles, interlocked together, have a certain amount of “give,” allowing them to move slightly. Such movement should not be too great, however. Excessive tie motion can cause the formation of “fines” which may harden into impervious masses, inhibiting drainage.
Types of rock
Over the years, a variety of materials have been used for ballast. Crushed rock such as granite and hard sandstone has long been preferred for main lines, and today’s heavy cars dictate that it be used even on light-duty trackage. Stones of 1 to 3-1/2 inches in size are preferred. Hard crushed furnace slag, some kinds of dense lava, and mine tailings have also found mainline use. In steam days, cinders were an abundant source of ballast; limestone, pit-run gravel, sand, and even crushed seashells have been used.
The average life of ballast depends on train frequency and weight. After the passage of about 250 million gross tons (2500 or so good-sized trains), it’s time for new rock, which is often simply dumped on top of the old, making the latter part of the sub-ballast, which need not be of as high quality as the top ballast. As the track must be raised each time this is done, this can lead to problems with vertical clearance, road crossings, and (where there is passenger service) station-platform height.
While the rock may have plenty of “structural” life left, it may simply be clogged with drainage — impairing debris — nothing a good cleaning won’t fix. As with most maintenance-of-way operations, ballast cleaning was at first a manual task; for several decades there have been a variety of rail-borne machines to clean ballast.
Ballast is transported from quarries (sometimes railroad-owned, mostly private) in special hopper cars whose bottom doors facilitate its precise dumping on either side of the rails. At the work site, ballast cars are moved along slowly by a locomotive, with track-crew members on the ground regulating the flow of rock by opening and closing the doors.
Railroads naturally prefer to move ballast as short a distance as possible. But if there is no high-quality rock nearby, and the cost of distant material is low enough, it may be worth the transportation expenses to haul rock in from hundreds of miles away.
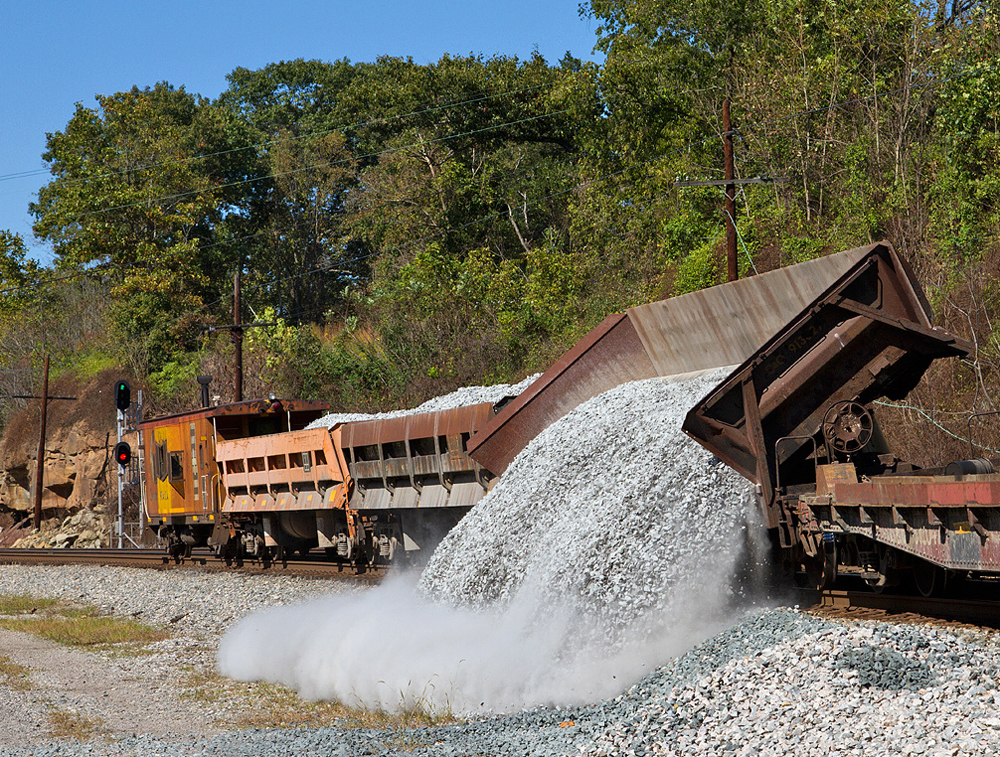
Great article. Very informative.