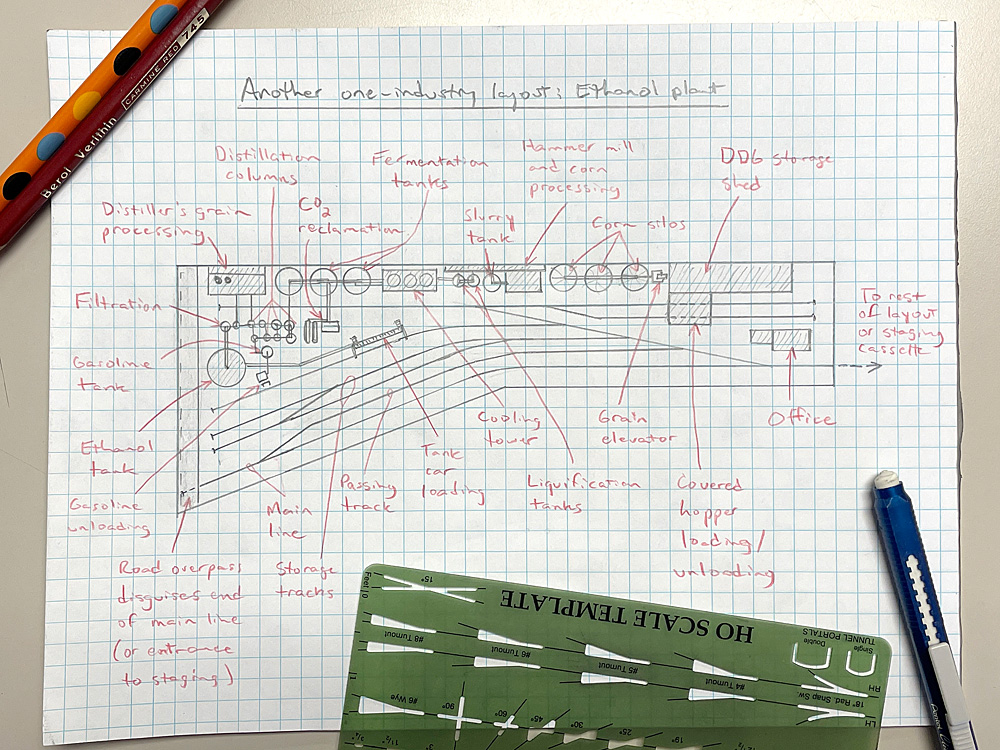
In last month’s “Sketching with Steve,” I explored a single-industry track plan by drawing a 4×8 paper mill layout. This month I’m doing it again, this time creating an ethanol plant track plan.
If you’re looking for a modern industry that offers lots of business for your model railroad, an ethanol plant is for you. Jeff Wilson wrote about the ethanol industry in his book The Model Railroader’s Guide to Industries Along the Tracks 3 (out of print, but used copies are still available in some online stores). In that book, he wrote that a typical 100-million-gallon-per-year (100 MGY) plant can receive 44 covered hoppers of corn and two tank cars of gasoline a week, and ship out 59 tankers of ethanol and 45 covered hoppers of dried distiller’s grain (DDG). Dried distiller’s grain is a leftover from corn distillation that is used in animal feed, and is an important product to the industry. That’s more than 20 cars a day, more than enough to keep a dedicated ethanol job busy during your operating sessions.
Though ethanol plants receive and ship a lot of cars a day, they don’t handle the variety of rolling stock that a paper mill does – just tanks and covered hoppers. So they don’t need as many tracks as my previous single-industry track plan did. Therefore, I decided to draw my ethanol plant track plan as a shelf that could either be operated stand-alone (with a staging/switching tail attached) or as part of a larger layout. What you see in my sketch above is actually my third draft, since I had to expand the footprint twice to fit in the structures I wanted to.
Let’s look at the ethanol-making process while we tour the layout. The raw material for most ethanol plants is corn. While some plants receive their grain directly from the farm via truck, others like ours get theirs from grain elevators via covered hoppers. The hoppers are weighed and unloaded in a shed to protect the grain from the weather, then stored in large metal or concrete silos. A winch system, Trackmobile, or tractor fitted with a coupler is used to keep the cars moving through the loading and unloading shed.
The grain is then ground into meal by a hammer mill, mixed with water and enzymes to break its starch down into simple sugars, and heated to kill any germs. After being cooled in a steam tower that looks pretty much like the ones seen at power plants, the mash is mixed with yeast in a fermentation tank. Some plants use continuous fermentation, in which the mash moves from tank to tank as the yeast converts the sugars to alcohol. Others use batch fermentation, in which the mash rests in the same tank until it’s ready. Either way, the process takes about 48 hours.
The fermentation process also produces carbon dioxide, which some ethanol plants simply vent off to the atmosphere. But others collect, purify, and sell it, adding an important revenue source to the plant.
The liquid is then run through a series of distillation columns, which work rather like those in an oil refinery. The distillation columns use heat to separate the lighter alcohol from the rest of the mash (now called, confusingly, “beer”). The beer is diverted to a processing building, while the now nearly pure alcohol is filtered and run through a dehydrator, resulting in pure anhydrous ethanol. To render it unfit for human consumption, it’s then mixed with about 3 percent gasoline by volume (which is where those two tank cars a week come into play). The final product is then stored in a large tank, painted white to reflect the sun’s heat, for loading into tank cars.
Meanwhile, the beer left over from the distilling process is sent to a processing building where it’s filtered, dried, and turned into distiller’s grain. Though the starches and sugars have been cooked out of it, distiller’s grain is still rich in other nutrients, making it a valuable ingredient in animal feeds. It can be sold to farmers and feed mills as is (called “wet distiller’s grain,” or WDG) and shipped out in trucks, or further dried to become “dried distiller’s grain” (DDG), which is dry enough to ship out in covered hoppers. It’s usually stored in a large shed and loaded into hoppers in the same covered area where grain hoppers unload. Different covered hoppers are used for the two different ladings, though.
My ethanol plant track plan represents a good-sized facility, though probably not in the 100 MGY range. A plant this size would probably receive four grain hoppers a day and ship out five tankers of ethanol and four hoppers of DDG. Once a week or so, it would receive one tank of gasoline and ship out one tank of compressed CO2. Once you add in pulling empties, this will keep those storage tracks full and a plant switch job quite busy.
Putting the hopper loading/unloading tracks on a switchback lets me make the best use of all the space on the layout, but it complicates maneuvers. The plant switcher or Trackmobile would have to make frequent use of the passing track off the main to switch those tracks. All the track on the layout, including the main, would probably be designated as under yard limits to allow such maneuvers without having to get a dispatcher’s authority. Luckily, switching the tank car track isn’t as tricky.
What structures might you use to build this ethanol plant track plan? Walthers has discontinued its North American Ethanol series of structures, but you still might be able to find them at a local hobby shop, train show, or online vendor. But even if you can’t, you have plenty of options. The large, generic industrial buildings of an ethanol plant could be kitbashed from Pikestuff corrugated metal buildings. Rix Products, which owns Pikestuff, also makes realistic looking corrugated metal grain bins and elevators. A large ethanol plant could be served by a concrete elevator like Walthers’ Prairie Co-Op. With the addition of some extra tanks, Walthers’ North Island Refinery and refinery piping set gives you the basis of the distillation system. A tank car loading platform gives you a place to spot those cars. Extra tanks, sheds, and pipes available from any number of vendors complete the scene.
Where can I find an HO scale track template like the one in the picture above? I’ve looked everywhere and can’t find one. Also, why do you often see crossovers at the end of tracks like on the two storage tracks in the diagram? Doesn’t make sense to me why you’d have a crossover all the near the end of the two tracks. Maybe I’m just not seeing something.