Crossties
Back in 1830, track structure was different from today: stone blocks supported wood stringers (or rails) surfaced with strap iron. During the harsh winter of 1832, shipments of stone blocks to the Camden & Amboy Railroad in New Jersey were curtailed. John L. Stevens, president and chief engineer of the railroad, ordered the substitution of crosswise wood slabs, to be replaced later. To Stevens’ surprise, the temporary crossties worked so well that he had the existing stone blocks replaced with wood.
Initially wood ties were no more than logs. It soon proved desirable to hew a flat surface on top to spike the rail to, and another on the bottom so the tie would stay in place. Eventually axe gave way to saw, and standard dimensions were developed: 6 inches high, 8 inches wide, and 8 feet long. They’ve grown somewhat since. Nowadays ties are 7 inches high, 9 inches wide, and 8 feet 6 inches or 9 feet long.
Preserving wood ties
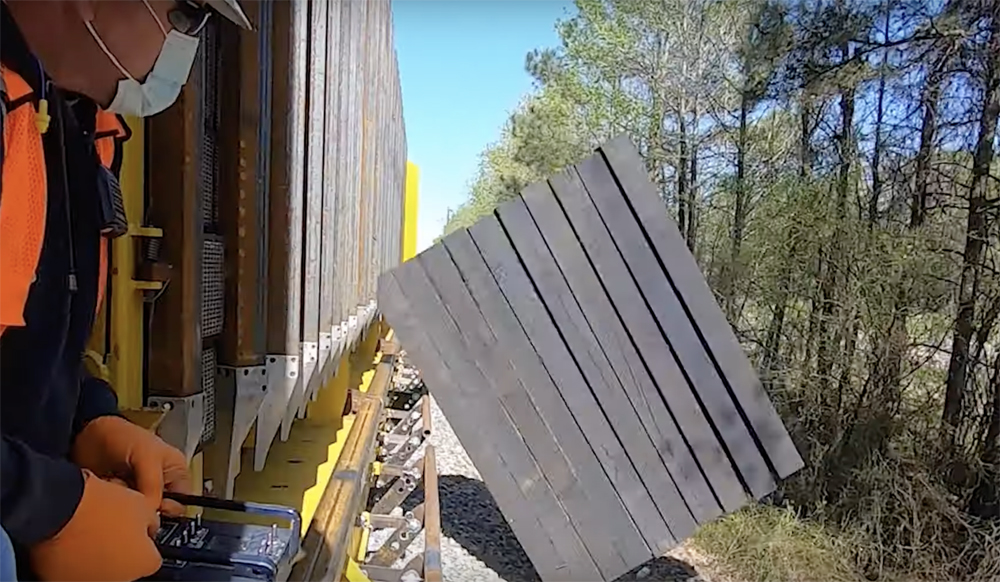
In the middle to late 1800s, most ties were hardwood. Oak was most commonly used, but even oak lasted no more than 5 to 10 years against the onslaughts of insects and fungus. In the 1840s the Cayuga & Susquehanna, an ancestor of the Lackawanna, tried soaking its ties in a salt solution, a practice that probably arose after someone noticed that pier pilings seemed to last longer in salt water.
The practice did not start a stampede of tie treatment, not with ties costing only 14 to 16 cents, delivered, and available for the cutting alongside the right of way in many areas. But as railroads pushed west, though, the supply of convenient timber thinned out considerably.
As the railroads began to understand the cost of replacing ties, they sought a way to make them last longer. The basic principle of wood preservation is that of forcing liquid preservatives into the wood under pressure. The preservatives protect the tie from insects and decay while maintaining its resilience and a high strength-to-weight ratio.
Ties treated with preservative last 15 to 20 years on lines with heavy traffic and 30 to 35 years on light-duty lines. Some time ago the Railway Tie Association discovered a tie on a former Baltimore & Ohio passing siding at Freedom, N.Y., that had been installed in 1912; the year was stamped on the head of a date nail, which railroads generally no longer use.
Creosote (more properly creosote oil) has been the lifeblood of the American wood treatment industry since the Louisville & Nashville started pressure-treating ties at West Pascagoula, Miss., in 1875. Previous treatment methods relied on zinc chloride, which tended to leach out (since chlorides are water-soluble).
If you’ve leaned against a pile of treated ties on a hot summer day you know that creosote is an oily, dark brown liquid. It is a complex mix of organic compounds obtained from the distillation of coal tar, which is a byproduct of the production of coke from coal. Coal is produced by millions of years of partial decomposition and compression of ancient vegetation, mostly plants that were similar to today’s evergreens and contained the same resinous materials.
Wood preservation essentially takes the materials that protected ancient trees and pumps it into the wood of today. Among the other materials used to treat wood are coal tar and petroleum. Clean, odorless materials are available where necessary — but not usually for ties.
Treating ties with preservative calls for more than a simple dunk in a vat of creosote. The first step in the procedure is seasoning, or removing the water from the wood. It can be done by simply drying the fresh-cut wood outdoors for six months to a year or by treating it with chemicals before the pressure treatment. After the water is removed from the tie it is replaced with preservative: creosote, perhaps, or a mixture of creosote and fuel oil. Ties are then bored for spikes, so that spikes will encounter treated wood, and incised — given little cuts all over — to help absorption of the preservative. Then they are placed in a retort, a pressure vessel, with the preservative and subjected to heat and pressure.
Other factors affecting wood ties
Railroaders differ on hardwood versus softwood — oak versus fir, hemlock, or pine. Some say that softwoods don’t hold spikes as well; others say that hardwoods don’t hold up as well under moisture and cold. Availability and price also influence the choice.
Other factors affecting tie life are spikes, tie plates, and ballast. When a spike is driven into a tie, it cuts the wood fibers, which bend downward and resist any upward pull on the spike. As the rail flexes under the weight of a train, it pulls upward on the spike. A spike can be redriven into a hole only so many times. Clips and fasteners of various types are replacing spikes on some railroads.
Rails don’t rest directly on ties but on a steel tie plate that spreads the weight of the rail and the train over a wider area. Ideally, the tie rests on ballast, a bed of crushed rock that allows water to drain away quickly and resists any motion of the tie. The sharp edges of the rock lock into each other and also into the bottom and sides of the tie, but they also cut into the wood.
Concrete versus wood
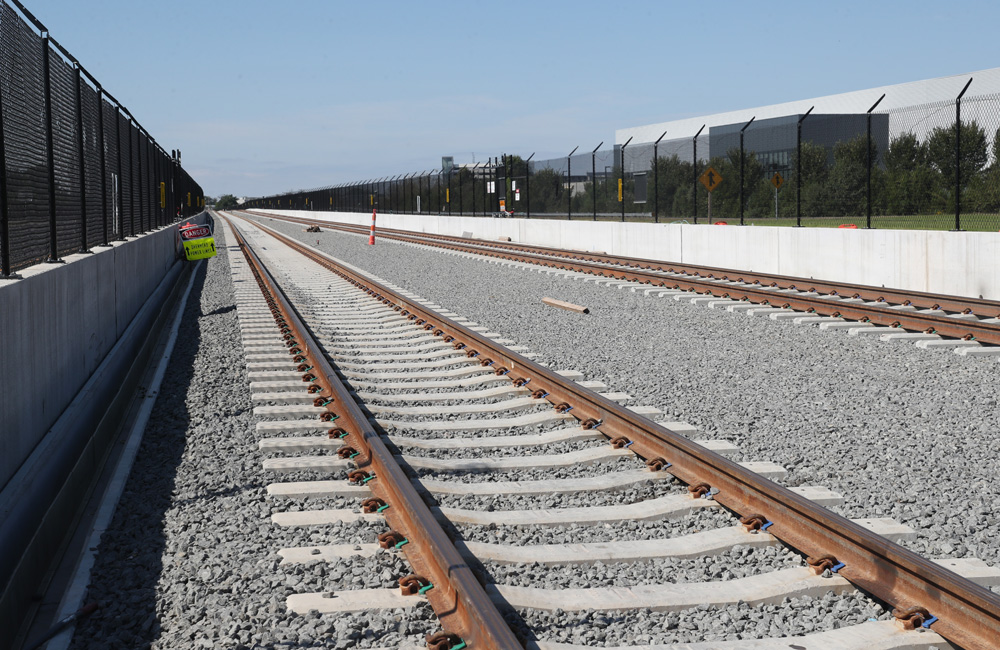
What about concrete ties? Popular overseas, they have found favor on some North American railroads, notably Florida East Coast, Amtrak, Burlington Northern Santa Fe, and Canadian National.
The wood tie is cheaper and lighter (260 pounds versus 600 to 800 pounds for concrete). Wood is resilient, and it serves to insulate the two rails from each other electrically — important for signal circuits.
Concrete lasts longer, and the combination of heavy ties and special tie plates and fasteners (ordinary spikes don’t work with concrete ties) makes a much more rigid track in which all components last longer. The unique shape of concrete ties, with the middle portion lower than the ends, was designed to best reflect the distribution of forces: a lot of material is placed where it is needed (under the rails), and relatively little is placed where the need is not as great (in the middle).
A footnote: Why are ties spaced as they are? W.M. Camp’s 1903 book, Notes on Track, says there should be enough space between the ties to allow a shovel to be used to advantage — at least 11 inches. This works out to about 20 inches on centers, about 10 inches less than the average person’s step.