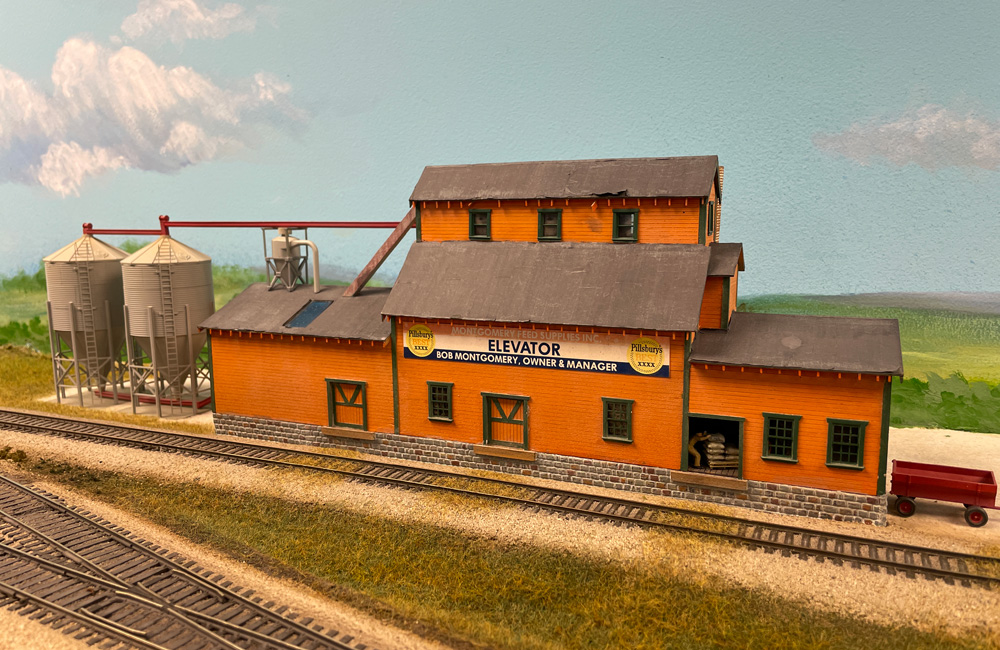
Q: I have acquired a vintage Suydam “Purina Chows” feed mill kit. What would be contained in the silo part of the building (grain or feed) and how did those feed dealers receive grain? Dumping grain from a boxcar seems a bit messy, and covered hoppers were not in use until the mid-1950s. I model the transition era up to 1955. I don’t think that individual sacks of product would be used to fill the silo. Was there a collection grate on the siding to deposit the material? – Tom Hiser, San Diego, Calif.
A: The Suydam kit represents a fairly small feed and seed dealer, with a modest-sized grain bin. The bin might have been separated internally into separate compartments to hold different blends of grain for feeding poultry, cattle, sheep, etc., but with a bin that small, it could have just held a single product.
It’s entirely plausible that such small feed dealers receive grain and seed exclusively in sacks – maybe one boxcar a week. In the time before covered hoppers became a popular way to ship grain in the 1960s, railroads hauled it in boxcars, either in sacks or in bulk, with the grain held back by grain doors nailed over the door openings. By either method, unloading was a laborious task, but labor was cheaper than machinery back then. So it wouldn’t have been unusual for a smaller business like Suydam’s Purina Chows to receive its wares in sacks and not have an unloading grate or chute. This is how Montgomery Feed & Seed, on MR’s HO scale Milwaukee, Racine & Troy house layout, operates. (Montgomery Feed & Seed was built from a Campbell Scale Models kit. See “Step By Step” in our August 2010 issue.)
Larger and busier industries received grain in bulk in boxcars fitted with grain doors. Made at first of disposable planks, then reusable plywood, then later inexpensive reinforced paper, grain doors were secured inside the openings of boxcar doors, covering them about 3/4 of the way up. Loading chutes were then poked through the openings and the grain was poured inside. Grain handling boxcars were marked inside with lines showing how high to load the grain, depending on its density, so as not to exceed the car’s weight capacity. When these boxcars arrived at their destinations, the grain doors were removed – with an axe, pry bar, hammer, or knife, depending on the material – and grain poured out. Workers then went into the boxcars with shovels to clear out grain that stayed in the corners. So while carrying grain in this manner was more efficient than in sacks, unloading it wasn’t that much easier.
How the grain got from the boxcars to the business’ elevator varied. Some had an unloading grate next to the building, alongside the tracks. This grate would be protected from dirt, weather, and vermin with ground-level doors that would be closed when not in use. Since a spectator’s view of the grate would be blocked when a car was spotted alongside, the grate itself need not be modeled, just the closed doors.
Other such businesses had even easier-to-model unloading methods. Sheller Feed Co., a prototype dealer that was the subject of an article in our August 2009 issue, had an unloading chute that folded down from the side of the building. When open, it extended under the doors of the boxcar, catching the shoveled-out grain and routing it to the base of the elevator inside the building. However, when it was closed, the chute looked like nothing more than a Y-shaped door on the side of the building. Adding a piece of stripwood representing a closed unloading chute to your Suydam kit would be a simple matter that would allow your business to receive grain in bulk.
For more information on how feed mills worked, see if your library, train store, or a member of your local train club has a copy of Jeff Wilson’s book The Model Railroader’s Guide to Grain. That book is out of print now, and although used copies are available online, they can get pretty pricey.
Send us your questions
Have a question about modeling, operation, or prototype railroads? Send it to us at AskTrains@Trains.com. Be sure to put “Ask MR” in the subject.