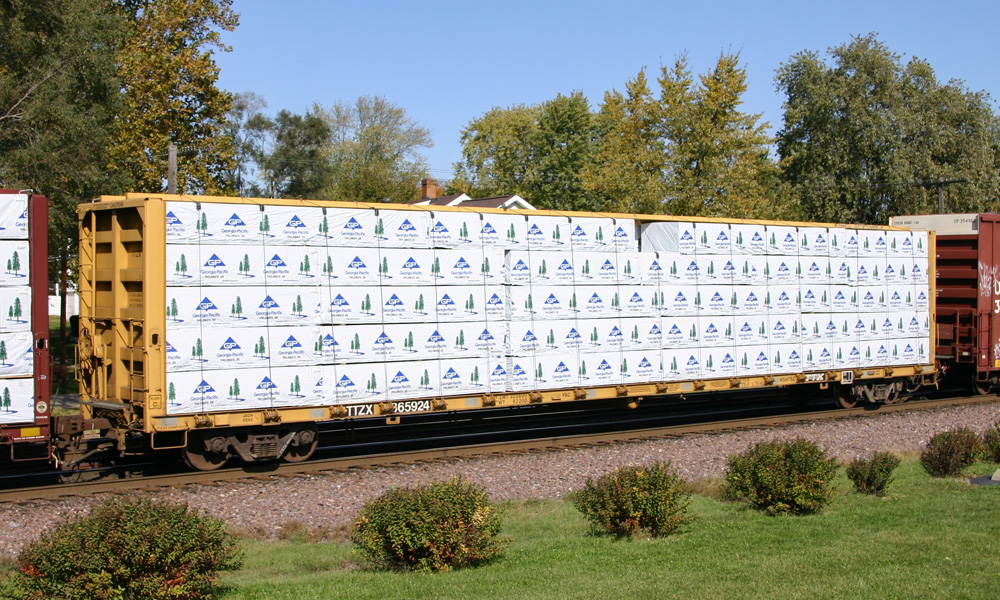
Q: I have made several stacks of scale 4 x 8 plywood for use as scenery on my HO scale layout. I place them as boxcar loads, but was wondering how lumber is shipped on the railroads? Was plywood in fact shipped in boxcars, or were other types of railcars used? – David Bellamy, Caledon, Ont.
A: You don’t say what time period you model, but how lumber is shipped depends heavily on your layout’s era. As Jeff Wilson writes in his new book, Commodities by Freight Car (coming in early 2023 – keep an eye on KalmbachHobbyStore.com), railroads have tried lots of different ways to ship plywood and other wood products over the years.
Wood and water don’t tend to get along well, so it’s always been important to protect lumber from the weather. In the early days, a lot of lumber was shipped in boxcars for this very reason. Unfortunately, this meant that the lumber had to be loaded and unloaded stick-by-stick (or in the case of plywood, sheet-by-sheet), a lengthy and labor-intensive operation. If the shipper wasn’t too worried about the effects of weather on the load – such as if it was low-grade lumber, or had been weather treated, or wasn’t going far – it was often stacked on regular flatcars or gondolas, secured with cables and stakes. But loads secured this way were at risk of shifting dangerously if the car lurched. Railroads started using bulkhead flats, originally developed to carry pulpwood, in the 1940s and ‘50s to carry lumber loads more securely. Although they helped keep errant lumber in check, the bulkheads reduced the weight the cars could carry, and the lading still had to be loaded and unloaded stick-by-stick.
In the early 1960s, how lumber is shipped started to change. Lumber mills started bundling wood products with metal bands, making it easy to load and unload in bulk using forklifts. Since bundled loads were less prone to shifting and could be stacked neatly, more lumber could be shipped more safely on each car. Bundling also greatly sped up the handling process, at least for lumber shipped on flatcars. But forklifts couldn’t easily navigate through 8- or 10-foot-wide boxcar doors while carrying a stack of plywood. So around the same time, the railroads developed double-door lumber boxcars and even experimented with “all-door” cars that could be opened all along their length. Though different designs were tried up through the 1970s, all-door cars proved to be more trouble than they were worth. Early cars were prone to flexing, which jammed the doors; later, heftier models solved this problem, but at the expense of heavy bracing that reduced their carrying capacity.
The answer was to return to the flatcar concept. Thrall built the first centerbeam flatcar in 1977. The centerbeam was basically a bulkhead flat with a tall steel beam from end to end. This design gave the car a lot of rigidity, allowing it to be built of lighter materials, which meant more revenue tonnage. Early models had oval cutouts in the middle of the beam to reduce its weight, but this gave way to a truss-style design that saved even more weight. Centerbeam flats have built-in straps that secure the load stacked on either side of the center beam, so no extra cables are needed. Once lumber mills started wrapping their weather-sensitive products in treated paper, Tyvek, or other such waterproof materials, centerbeam flats have been how lumber is shipped since the late 1980s.
Centerbeams are usually stenciled with warnings to load and unload them evenly on both sides of the beam to prevent them from becoming overbalanced and tipping. Facilities for loading and unloading centerbeams are therefore usually flat areas with paving on both sides to allow easy access all around for forklifts.
Send us your questions
Have a question about modeling, operation, or prototype railroads? Send it to us at AskTrains@Trains.com. Be sure to put “Ask MR” in the subject.