It makes good sense to maintain your large-scale equipment. Basic maintenance is the key to reliable operation. There are several simple things you can do to keep your trains running through the garden.
Basic locomotive maintenance
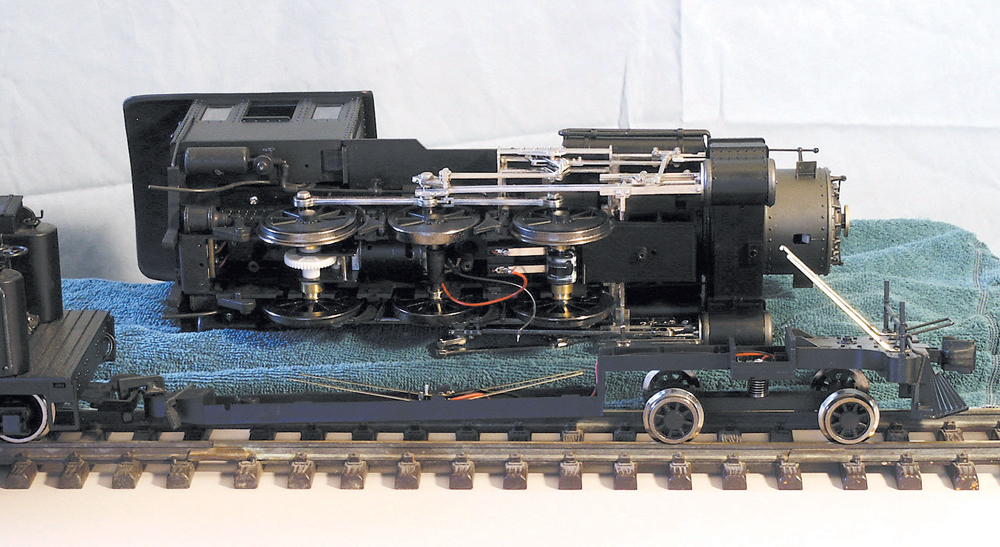
Many manufacturers include exploded drawings or written instructions on how to properly lubricate the gears. All moving parts should be kept lubricated. Gears should be coated with a plastic-compatible grease. If the main gears are allowed to run dry, they will be prone to stripping, accelerated wear, and even breakage.
Wheel bearings should be oiled occasionally with a touch of sewing machine (or similar) oil. WD-40 is not an acceptable lubricant. It’s great for freeing up rusted bolts but has no long-term lubricative properties.
Occasionally put a drop of oil on the valve-gear joints of steam locomotives. This routine oiling isn’t something that has to be done before every run. Depending on how often you run, once or twice a year is adequate. The grease on the main gears tends to stay put for longer periods of time because, in most cases, the gear boxes are sealed. Oil on the bearings and valve gear tends to evaporate or dry out more quickly and may need to be replenished more often.
Don’t bathe the parts in oil. A little drop will do quite well.
Proper electrical conductivity is essential for good operation. Cleaning needs to be done a little more often than lubricating, depending on your operating environment. The key areas that need to be kept clean are the wheel treads and the point at which power is transferred from the wheels to the brushes or wipers that carry electricity to the motor.
Some manufacturers suggest coating the wheels with a conductive lubricant. I’m not a fan of putting any kind of liquid on the wheels, as this invites trouble. Dust can be picked up as the locomotive runs down the track. This dust not only gets in the way of electrical conductivity, but slowly grinds away the surface of the wheel and the rail as it’s run over by the train.
My favorite tool for cleaning wheels is a fine Scotch-brite pad. Avoid sandpaper, as this creates microscopic grooves that collect dirt and grime.
The best recipe for keeping wheels clean is to keep the track clean. Equipping your rolling stock with metal wheels goes a long way toward facilitating this, as it eliminates the plastic buildup that can cause conductivity problems.
Basic rolling stock maintenance
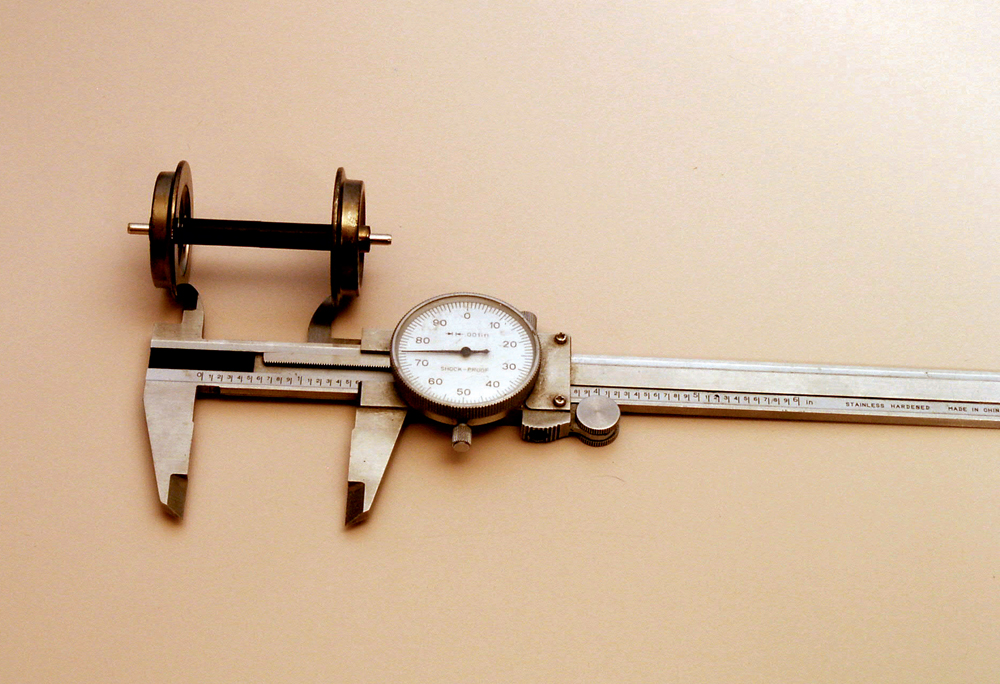
Wheels need to be properly gauged to provide smooth operation. The standard back-to-back spacing for wheels running on Nº 1-gauge track is 1.575″.
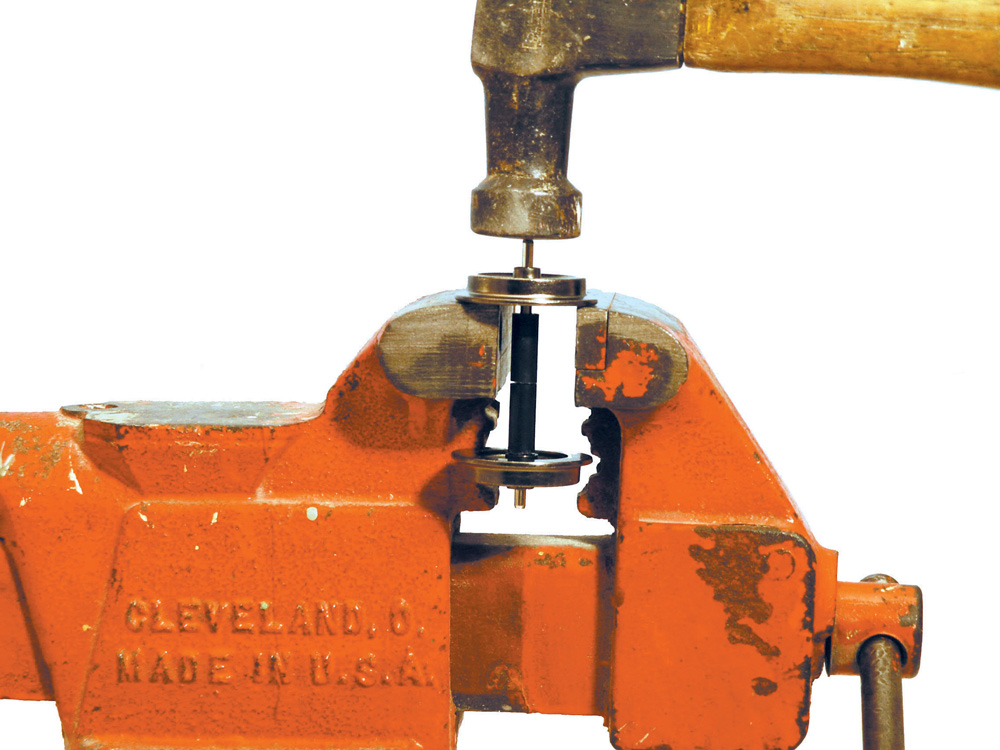
It’s more common for wheels to be too close together. This can be fixed by resting the wheel on the jaws of a vise and tapping the axle lightly until the wheels are the proper distance apart. Wheels that are too far apart may be more difficult to correct, as you may need to remove some material from the plastic axle to allow them to come into gauge.
Another malady is a wheel that doesn’t sit squarely on its axle, giving it a wobble as it rolls. For metal wheels, light tapping with a hammer may correct this problem. If it’s a plastic wheel, replacement is commonly the only solution.

Once the wheels are in gauge, make sure the trucks they’re mounted in are in good shape. A drop of plastic-compatible oil on the ends of the axle will lubricate the journals (the boxes on the truck in which the axles rotates) so the wheels turn freely. Make sure there is a slight amount of lateral play in the axles. If there isn’t, that means the journals are pressing in on the axle ends and the axle won’t rotate freely.
This can be fixed by drilling out the ends of the journals ever so slightly. Be careful to use a drill that is the same size as the existing hole. Don’t enlarge the diameter, just make it a little deeper.
Too much lateral movement, however, can also lead to trouble. The axles could pop out of the journals, causing a derailment. Thin washers placed on the axles between the wheels and the journals can help by limiting the amount of play between the journal and the hub of the wheel.
Check the attachment of the trucks to the car. Trucks need to be loose enough that they can turn freely, but not so loose that the car wobbles on the track. I try to keep one truck tight enough that the car has movement back and forth longitudinally, but not side to side, while the other truck has a little side-to-side play. This allows the car to roll better over uneven track without danger of derailing.
Great article from Kevin! It is very helpful for those of us who have a fleet of older locomotives and rolling stock. More of these please.